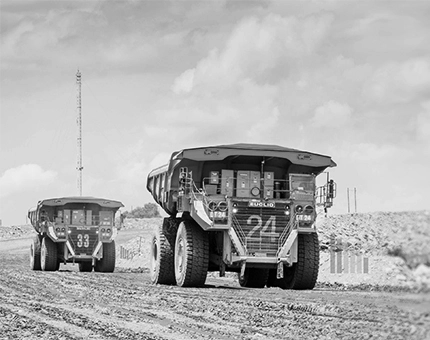
MaxMine roads leads to site-wide, safe speed limit increase – resulting in 10KM/HR rise in maximum speed for both haul and returns.
The projects team were able to successfully utilise Haul Road Conditions as an input into their scheduled road maintenance plan. As a feedback tool for continuous improvement it eliminated any subjectivity around road conditions through its method of measure.
Mine Production Engineer
Issues On Site
In early 2019, a MaxMine client embarked on a campaign to improve haul road conditions on site after realising that a poor haul road network significantly impacted multiple productivity levers, including haul/return cycle times, machine health, maintenance time and cost.
Improving operator performance and productivity relies on setting the team up for success – providing a level playing field (roads!). The end result is always to increase tonnes, safely and profitably.
MaxMine Application
Through automated analysis of operational data, road conditions and road management activities, MaxMine Roads provides insights to help sites actively manage targeted areas of a client’s operation to deliver measurable improvements.
MaxMine was able to provide the client with detailed Haul Road Condition (HRC) reports that enabled supervisors to identify the ‘roughest’ haul road sections most in need of improvement.
Using heatmaps, areas of roads to be worked on and improved in the upcoming shift(s) were clearly identified.
To do this, MaxMine combines and analyses multiple data sources used to calculate HRC, free from human input.
- Haul truck strut pressure signals are used as a road roughness assessment tool as the truck traverses haul roads during their normal operations. Road roughness is then categorised as Smooth, Light, Moderate, Rough and Extremely Rough, showing clearly which roads need attention.
- Grader activity, vibration and engine parameters are used to determine the difference between grading and transit activities showing clearly what work has been completed.
- Water truck activity and spray valve actuation is used to assess areas where roads have been sprayed.
HRC reports, such as the heatmaps, can be exported directly to pdf – making it simple for grader operators to know where to focus. MaxMine Roads can even detect and determine the effectiveness of grader operators, for example; Where did the grader spend its working time for that shift? Was it focused on the areas that required maintenance?
Finally, all of the above data was reviewed and assessed to determine whether the work made a resulting difference at the client’s site – both to HRC and then productivity.
Results
18.2%
Returns: From 22.5km/h±4.3km/h to 26.6km/h±6.4km/h
16.5%
Hauls: From 34.6km/h±1.4km/h to 39.7km/h±2.2km/h
The average circuit transit speeds also showed a slight rise following the speed increase.
11.7%
Returns: From 23.0km/h±5.4km/h to 25.7km/h±6.3km/h
4.4%
Hauls: From 15.9km/h±1.5km/h to 16.6km/h±1.5km/h
The increase in circuit speed although small, represents a significant improvement in load and haul productivity.
Applicability to the industry and other sites
Haul Road Conditions is just one of the many productivity levers identified in MaxMine’s Value Driver Tree (VDT). The MaxMine VDT is a powerful tool applicable for all load and haul operations, allowing mines to visualise, understand and address key metrics impacting productivity on site.
Good haul road condition is therefore fundamental to mines being able to meet production targets. MaxMine has also been deployed on a mining fleet that included a large number of graders however the graders were low-tech with no operational data. With graders used as a primary tool for maintaining haul road conditions, MaxMine worked with the client and used the millions of hours of operational data it has captured and developed a machine learning model to deliver an automated activity classification report. This report turned masses of data into meaningful knowledge that the client could act on and improved grader utilisation by 35%.