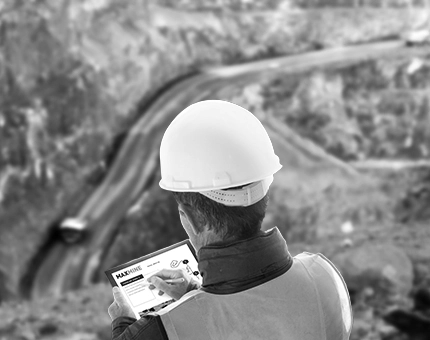
A client was exceeding their budgeted engine hours while not achieving target tonnes hauled. Pursuant to this, an in-field observation suggested that queuing was occurring, however, data from the fleet management system could not substantiate this observation. Management suspected that dispatch operators were manipulating their KPI’s by manually changing delay codes (queuing) to standby codes (waiting by shovel).
MaxMine Application
MaxMine began by automatically distributing customised dashboards to make the magnitude of the queuing problem visible to all stakeholders. Parallel to this, MaxMine coaches were deployed to aid the client in improving how queue times are managed during normal operations. The coaches reviewed and updated standby and delay codes to improve efficiency with which the fleet management system allocates trucks. To ensure long term sustainability the dispatch team were trained as to how to manage queue times during the shift. With MaxMine’s implementation and changes the client was provided with a single version of the truth, thereby eliminating the loophole to manipulate KPIs.
Results
16%
reduction in overall queue time while total number of hauls remained the same
$240,000
Annualised savings ($240k saved in the first 35 days post implementation)